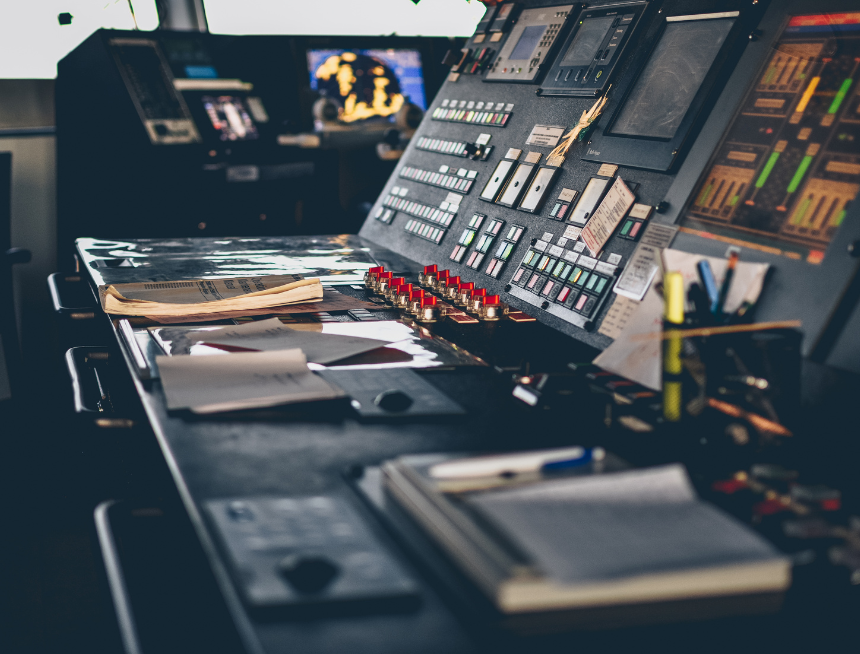
90%
reduction in manual packing errors with custom cartonization workflows
100%
automated EDI document generation (ASN, Invoice, SSCC) from NetSuite
4x
faster post-fulfillment processing through a centralized NetSuite interface

About
Client
Business
Brand Insights
Legend Linen is a renowned Australian bedding design wholesale company delivering high-quality, trend-forward home textiles to major retailers and partners.
Store Presence
The company manages high-volume warehouse operations and EDI-based order fulfillment processes for retail clients across Australia.
Operational Challenges
The client struggled with tab-switching for warehouse tasks, manual and inconsistent cartonization, the absence of standardized packaging rules, and delayed EDI document generation, all of which hindered efficiency, accuracy, and fulfillment speed.
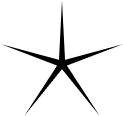

Our Solutions
Our team developed a customized, user-friendly NetSuite interface to manage the entire post-fulfillment workflow, spanning from item picking and packing to cartonization, label generation, and EDI document automation.
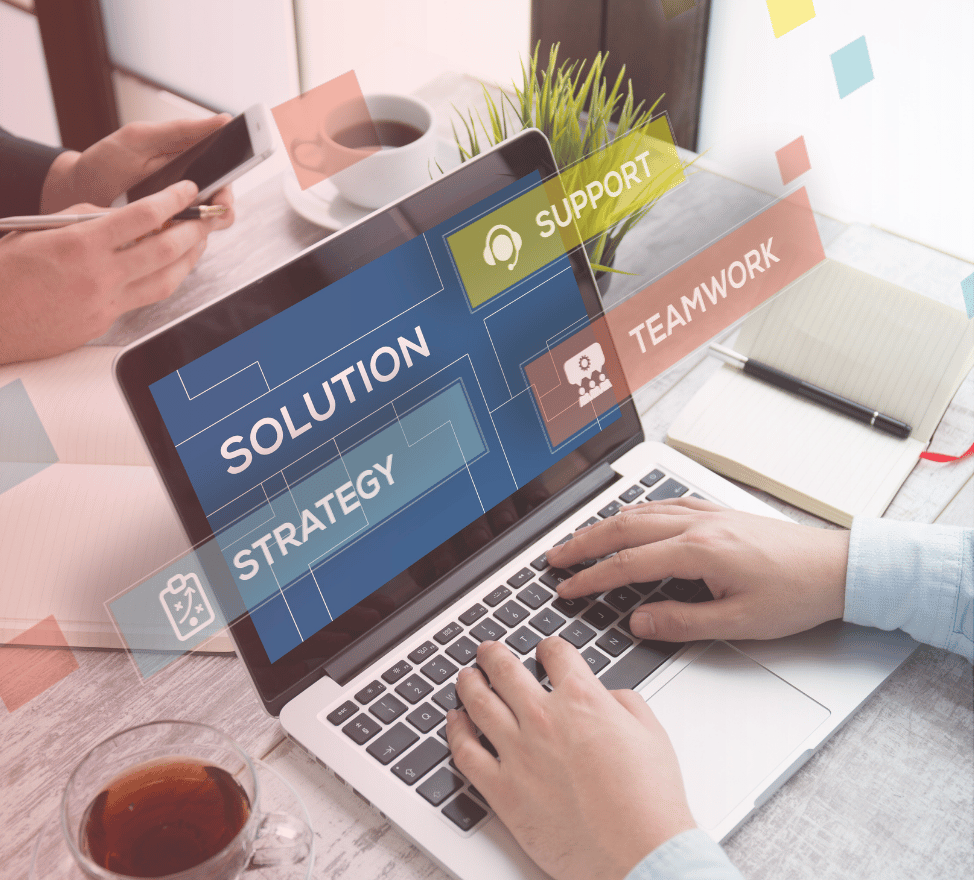
Unified Cartonization Interface
All fulfillment activities, such as carton creation, SSCC label printing, ASN, ASIN, and invoicing, are managed from a single interface, enabling a seamless transition from fulfillment to shipment.
Custom Cartonization Methods
The interface supports four user-controlled packaging methods, i.e., Single Carton, Consistent Carton, Mixed Carton, and Auto-Pack Shipment, allowing flexibility and control based on order size and product type.
SSCC Label Printing via Suitelets
Custom SSCC labels in GS1-128 format are generated instantly after cartonization using Suitelet-based tools, reducing time and ensuring compliance with retail partner requirements.
ASN Generation Automation
Once cartonization is completed and SSCC labels are generated, the system automatically triggers consolidated ASN creation across fulfillments, streamlining the outbound EDI process.

Challenges
Streamlining warehouse packaging and EDI operations for improved efficiency.
Manual Cartonization and Workflow Gaps
Packing processes were manually executed across multiple tabs, causing delays, inefficiencies, and increased error rates in warehouse operations.
Lack of Standardized Packing Rules
Inconsistent packaging logic led to non-uniform cartons, space inefficiencies, and missed opportunities for shipment optimization.
Delayed and Disconnected EDI Documentation
ASN, SSCC, and invoice generation were not unified, resulting in slower processing times, reduced accuracy, and poor visibility across fulfillment stages.
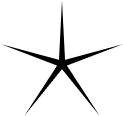

Results
The NetSuite-driven EDI fulfillment and cartonization interface led to major gains in efficiency, accuracy, and user experience.
Improved Packaging Accuracy
Standardized cartonization logic reduced packing errors and ensured consistency across all order types.
User-Friendly Interface
A single, intuitive UI empowers users to manage fulfillment, cartonization, labeling, and invoicing without switching screens.
Real-Time EDI Processing
Immediate generation of SSCC labels, ASNs, and invoices enhanced order processing speed and reliability.
Seamless Workflow Integration
Fully automated and integrated post-fulfillment processes streamlined operations and minimized manual intervention.